GE Transportation Alternator Lean Line Lift System
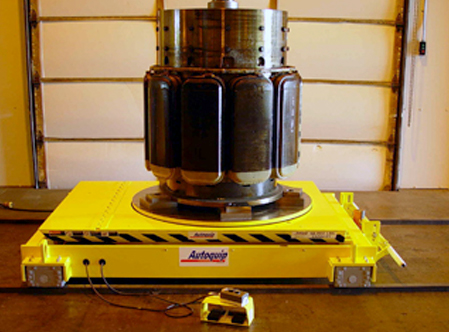
Introduction
Autoquip’s custom lift system improves production assembly of GE alternators.
Project Challenge
General Electric Transportation contacted our dealer, David Snell from Materials Handling Enterprises for a solution to speed up their manufacturing process for their alternators. They wanted to create a lean line system to move the process along more efficiently and work smarter.
Our Solution
In working with our dealer to understand the customer’s application requirements, we developed a lean line lift system to include:
Station #1: (1) Flip Flop 90° Upender with a powered ring bearing turntable and special tooling to hold yokes for assembly, 9K capacities with a special airlift that will lift coils to be assembled on the yokes.
Station #2, 3, 4, and 5: (4) transport bases with powered ring bearing turntables. 16k capacities each with 6” travel up. (1) Chain driven towline conveyor by Webb Stiles to move all (4)-transport bases down the line for assembly to make yokes into rotors.
Station #6: (1) Flip Flop 90 ° Upender 26k capacity with special tooling. This station completes the alternator. The big casting is put over the rotor and then upended to be taken away with a crane.
The Results
We were able to partner with our dealer to understand the customer’s every requirement to build a custom lift solution to meet their production demands. The lean lift system has helped improve the customer’s operations and speed up production of their alternators.